As Kenji Matsuura walks me through Matsuura Blast, a machi-kōba (small city workshop) in Tokyo’s Katsushika Ward, he gestures to various plastic crates. “That’s our normal work,” he says of their contents — stacks of glasses, all prepped to be sandblasted with logos and motifs.
Matsuura Blast specializes in the art of “sandblasting” – abrading texture and designs onto glassware and other objects. Its oeuvre runs the gamut, from batches of decorative tumblers and bottles to sports tournament trophies and special small-lot orders. But, as Kenji explains, that opaque, frosted satin finish we see on so many products is not always a simple process. It involves impeccable timing, an experienced feel for the materials and patience.
One example is the Tokyo Keyboard project, where they used sandblasting to create a frosted finish on a mechanical keyboard. Much of the work can be really “mendokusai” (“bothersome” or “annoying”), as Kenji likes to jokingly stress while he shows me the factory and explains the ins and outs of the sandblasting business.
This interview has been translated from Japanese. It has been edited and condensed for clarity.
⎻⎻⎻⎻
Your factory is in Katsushika Ward, an area of machi-kōba historically related to the toy industry. Why there?
My grandfather originally worked in Ryogoku before he started his own business in Kinshicho. Both those areas are in Sumida Ward, (a district known for glass factories). I’m actually not sure why but at some point, he decided to move to Katsushika. Katsushika’s a great place to be based in though – there’s a diversity of industries that makes it a great cooperative community. We’ve been here for 30 years now.
Why specialize in sandblasting?
We’ve actually only been doing that for around for 36 to 37 years. My grandfather, though, worked a long time with the glass industry as a wooden glass mold carver. It was when steel molds began to replace wooden ones that my father realized we needed to adapt the family business to survive. He’s the one who decided to focus on sandblasting.
What about you — how did you get into the business?
Well, I really disliked school, so as soon as I finished junior high, I began apprenticing under my father.
How did you learn the craft?
I was taught on the job by other craftspeople at the company, and I remember being scolded was also a way of learning. I was 15, and I admit there were times when I didn’t want to do it.
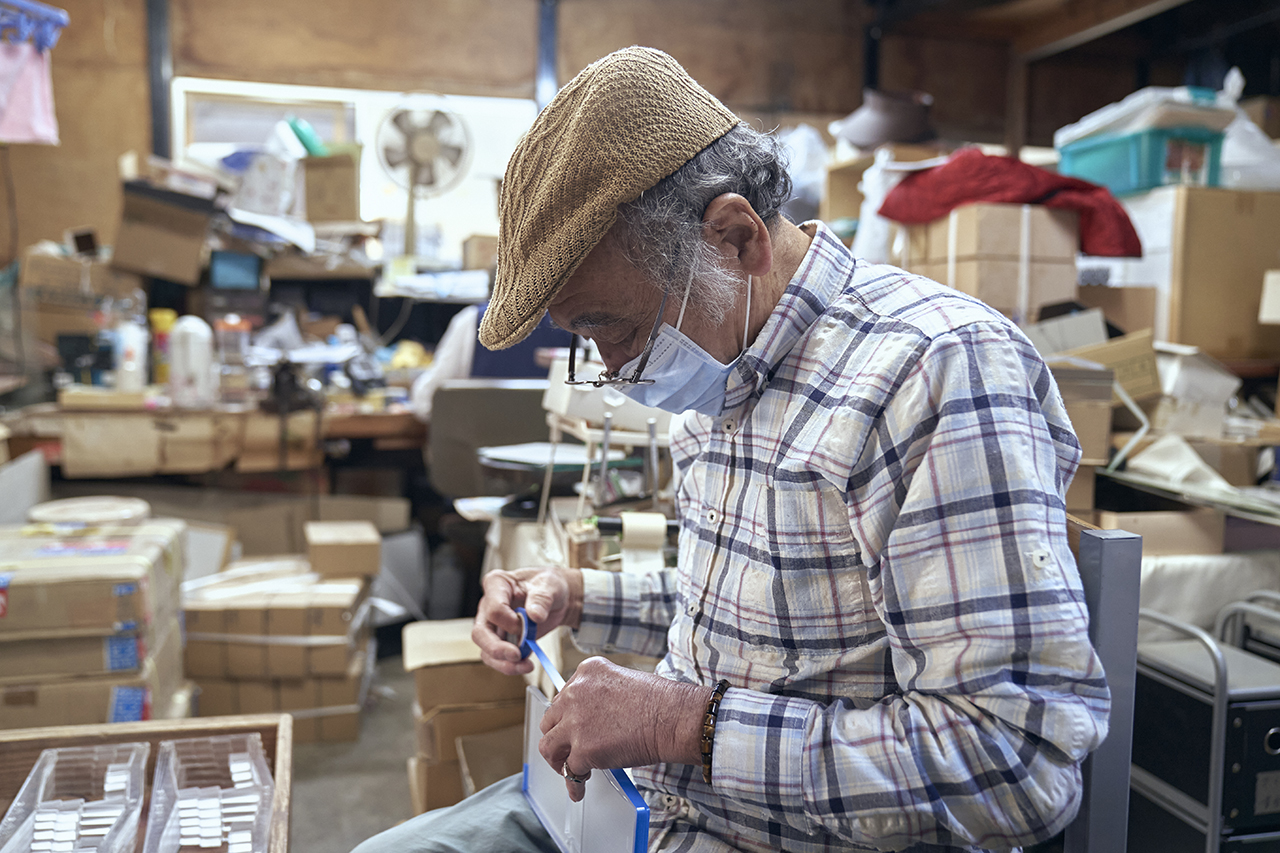
For those not familiar with it, what exactly is sandblasting?
Essentially, transparent material, like glass, is incrementally abraded by grains of sand or tiny beads. The actual transformation to a frosted texture can happen really fast — in a matter of seconds. Designs or patterns etched onto glass, for example, change with each second of sandblasting. Even a microsecond can make a difference. Our job is to execute and time it perfectly — that requires technique and experience.
So this involves specialized machinery?
Yes, our equipment is made in Japan and some of the machines date back more than 50 years to when my dad started his business. Truth is, not much has really changed since then. New machines are not that different to those from decades ago. In fact, the company that made ours, still makes the same ones, and we have never had a problem with them as we maintain them regularly.
But there are processes done by hand.
Pressurized air is needed to manipulate the sand, so that’s usually done inside a cabinet sandblasting machine. Everything else, though, such as handling the product inside the machine, is guided by the craftsperson’s intuition. The finish of the product all depends on that person’s instinctive use of the machine and their affinity for the product material.
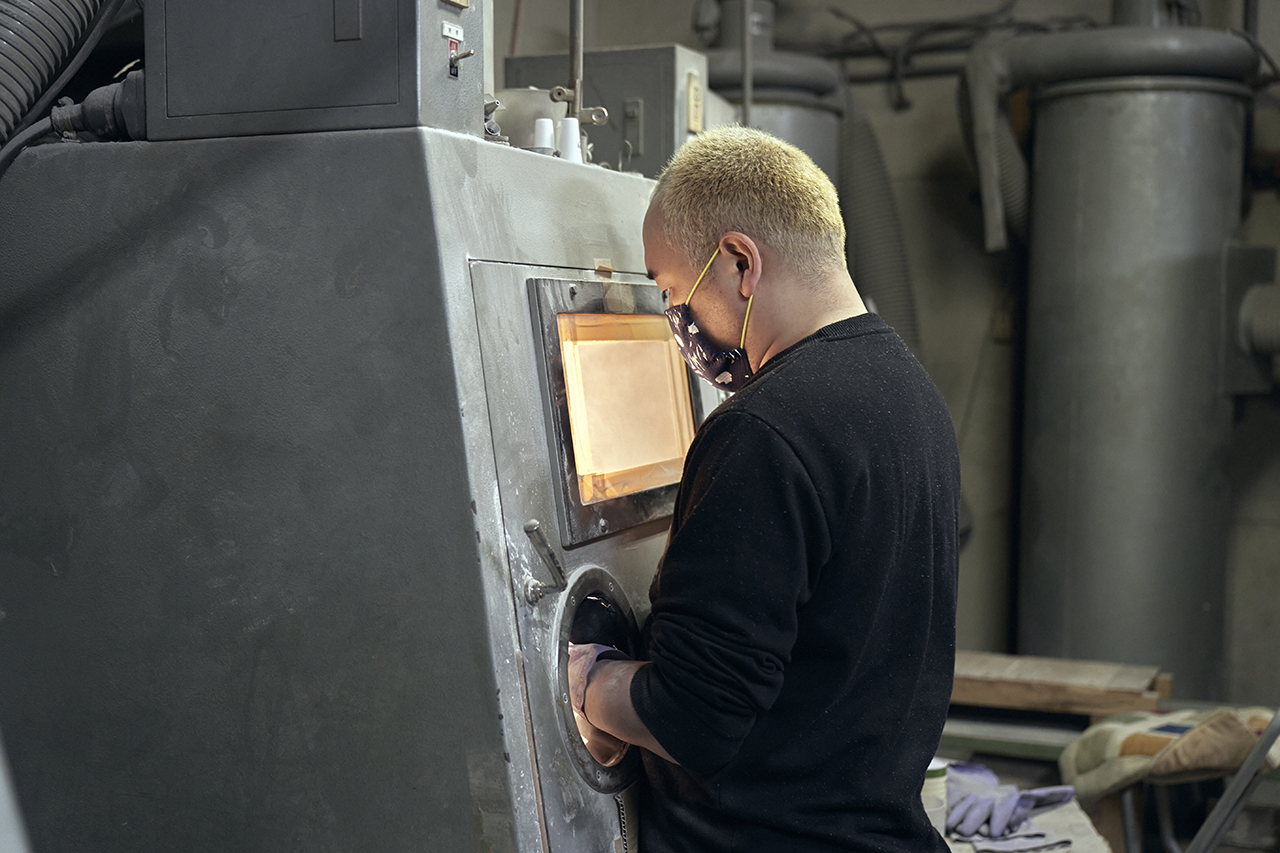
I’ve heard of glass beads used for blasting, does that do something different?
We mainly use sand, but there are times when glass beads are useful. Sometimes, natural oil from our hands ends up on the product we are working on — then we use glass beads to remove that. In general, though, we stick to sand.
What kind of things do you sandblast?
We work with clients’ products, and our role is to realize the clients’ artistic visions onto their glassware. We get the designs made into vinyl film stencils, which we applied on to the glass before sandblasting.
Some of our customers create new products, but we also work with a lot of bottle makers, glass distributors and wholesalers, including those for department stores. So that’s the main part of our business. I also work with other materials, such as steel, other metals and wood.
You’ve also worked with acrylic for the mechanical keyboard brand Tokyo Keyboard’s latest keyboard. How was that?
When we were asked to sandblast acrylic parts to be dyed, I was quite skeptical. I wasn’t sure what the goal was. But when I saw the end result, it dawned on me, “Oh, that’s what it eventually turns into!” It was very enlightening. From now on, I’ll try to be more optimistic in my approach to unusual projects, haha.
Working with acrylic does have its annoying quirks, though. Sandblasting will make it white and frosted, but it’s very different to glass. When glass is abraded over time, it just creates indentations, but if you sandblast acrylic for too long, it gets burnt. It’s a tricky process.
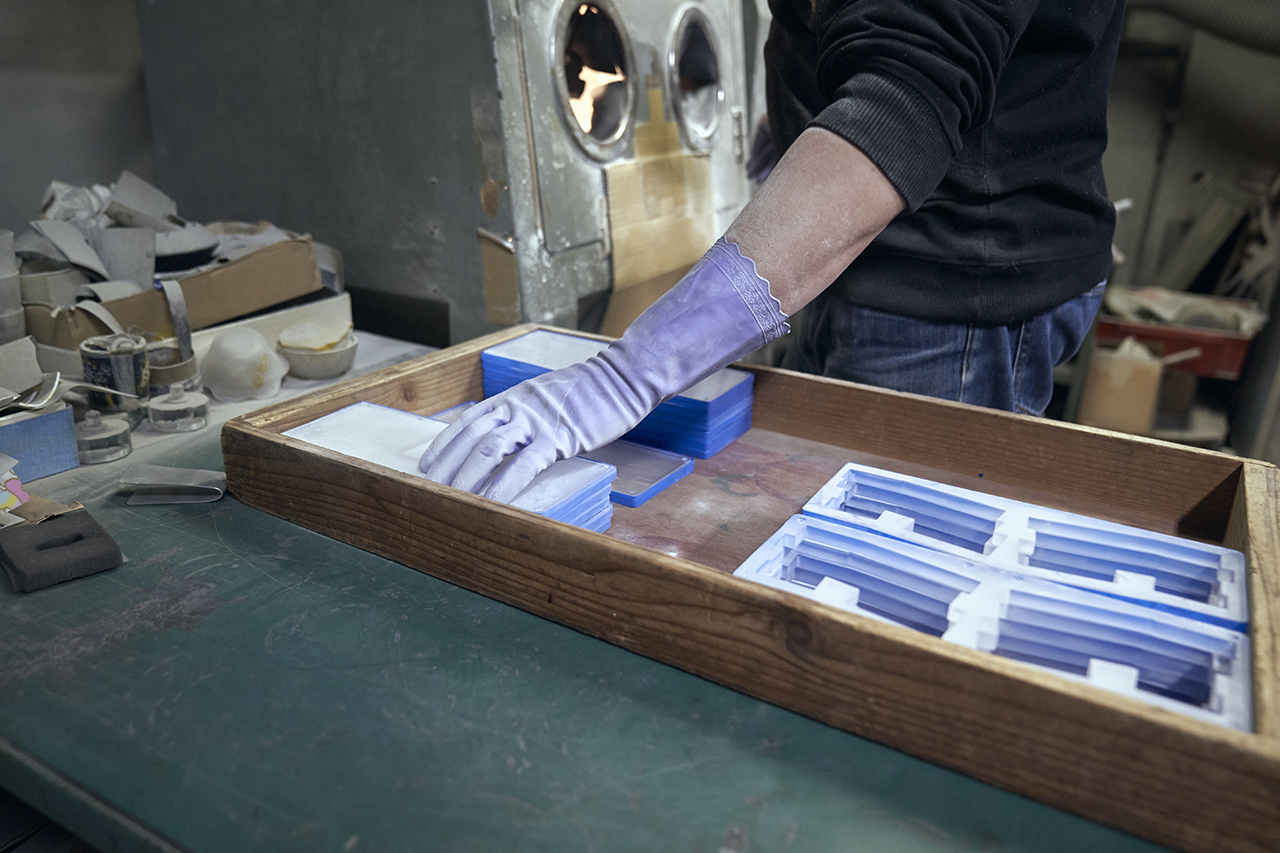
What about really large objects — how do you sandblast those?
If it’s big, and I mean really big, I do it onsite. For example, I sandblasted a large outdoors display figure at Disneyland to clean it. That was 4-meters tall. I’ve done that about ten times at least, haha. I had a giant globe-shaped vinyl tent constructed to house the figure, and attached a sandblasting machine to it. Then I had to wear a protective suit and get inside the tent to do the work. To be honest, I didn’t like going inside — but if I have to, yeah, I’ll do it.
Are there any other unusual items have you worked on?
You know the chair that the Japanese Emperor sits on? The one you see a lot when he’s on TV. There’s a specific component that’s attached to its backrest that we worked on. I guess we are involved in a huge variety of things...
Of those things, what was the most difficult project you’ve taken on?
That has to be a watch for Seiko Epson. I had to sandblast characters onto the glass, and the depth was already decided beforehand. Each amount I needed to abrade away was just a fraction of a millimeter, so it was quite vexing and hard to do!
You say it was somewhat annoying, but you seem to revel in the challenge…
As a company, we enjoy seeing what kind of work and projects clients bring to us. Getting asked if something unusual is actually feasible, and then figuring out how to achieve it — yes, it can be a real pain in the butt. But when it’s successful, like the Tokyo Keyboard project, it’s worth it. It can potentially lead us to other discoveries. ▲